Roll forming needs a suitable material to produce the best product at the right price. It is difficult and essential to choose the appropriate material for a job. Designers and material specifiers must consider many factors.
You need to know what a roll-forming machine can do to help you get your project started. While most people understand that material thickness is essential, this is only the beginning.
This guide is for people who don't know much about roll forming,
What Is The Engineering Procedure For Roll Forming?
After the concept has been developed by an industrial designer and the volume/cost estimates have been validated for the application, design engineers will convert the part design into final specifications for manufacturing,
These manufacturing considerations are similar to aluminum extrusions or sheet metal processes. Roll-formed metal designs should have some symmetry, just like aluminum extrusions. While this is not essential, it helps ensure that the form is carried straight through the roll-forming line.
Roll Forming Stainless Steel
1. Mechanical Properties
Any product must safely withhold the maximum load expected without deformation and stay within the prescribed deflection. The material's mechanical properties and strength are critical factors in determining the resistance to the bag.
Elongation, yield strength, and tensile strength are the most important mechanical properties. Tests are used to establish these properties. Materials are tested for their mechanical properties using tension.
The specimens to be tested are then cut from the material. The illustrations are then placed between the jaws on a machine that measures their cross-sections. Next, the gradually increasing load and the length are checked.
2. Formability
The yield stress is never reached in well-designed products. The maximum load does not permanently damage products. Permanent deformation can only be caused, such as the crashing of a vehicle or the overloading of a structure.
All metals must be rolled formed with stress levels above the yield stress. Material that is created using a pressure lower than yield will return to its original form.
The maximum tensile stress will cause cracking and tear in the product if the forming stresses exceed this limit.
3. Strength
A material's yield and tensile strengths can usually be increased through hard work, alloying, heat treatment, or combinations thereof. A wire can be broken if it is bent repeatedly at the same spot.
Cold working is what causes the breakage. Each bend makes the wire harder, and its elongation decreases until it can no longer withstand hard work.
This same phenomenon happens when metals are rolled. The metal strip is passed through two rolls with decreasing gaps to achieve the desired thickness.
4. Other
The sheet metal industry does not use pure iron. All commercially available steels contain a small amount of carbon and other impurities that are absorbed by iron during steel-making.
A small number of impurities such as sulphur and phosphorus can impact the steel's properties. These impurities must be controlled.
These questions will allow you to make the right decision about the metal that you should use to form your roll-formed product.
Also Read: Hot Vs Cold Roll Forming
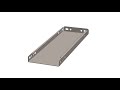
No comments: